The Art of Plastic Molding - Exploring 6 Essential Techniques
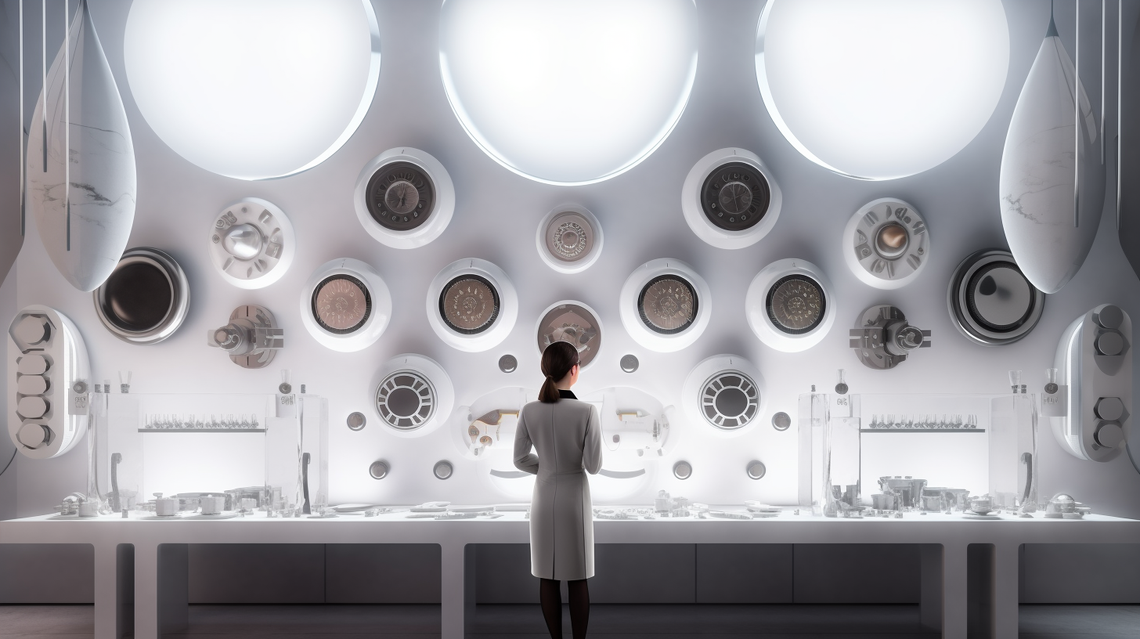
Plastic molding - it's in our cars, our water bottles, and even the chairs we lounge on. Let's dive into the nitty-gritty of the techniques used in crafting these everyday items.
-
Injection Molding Perhaps the most ubiquitous method, injection molding, transforms plastic resin pellets into liquid form through heat. This is then injected into a mold under extreme pressure. After cooling and solidifying, the mold reveals a precisely formed part. Known for its swift production speed, accuracy, and minimal waste, this technique is perfect for mass-producing intricate plastic parts, making it a darling of industries such as automotive.
-
Blow Molding Ever wondered how hollow items like bottles are made? Enter blow molding. In this process, melted plastic forms a parison or preform for Injection Stretch Blow Molding. A parison is a spherical mass of molten material crafted immediately after removal from the furnace.
Next, air inflates the parison into the shape of the intended object like a bottle or jar, which is then ejected upon cooling.
-
Rotational Molding Rotational molding caters to the creation of large hollow items. The plastic resin fills a mold, which is then heated and rotated on two perpendicular axes. The melting plastic coats the interior of the mold, crafting a hollow item. Commonly used for larger, one-piece objects like farming products, kayaks, and other equipment, this process is slower but more economical for small production runs.
-
Compression Molding In compression molding, the plastic is preheated and inserted into a molder. Pressure is then exerted to compel the plastic to assume the shape of the mold. Once cooled and solidified, the part is ready. This technique shines in creating robust parts needed in automobiles and electronics. It's also popular for thermoset plastics and precision parts requiring high-quality finishes.
-
Extrusion Molding Extrusion molding heats plastic and propels it through a die, resulting in a long product with a uniform cross-section. The product can be cut to the desired length upon exiting the die. Ideal for creating uniformly shaped long plastic parts like pipes, tubes, window frames, and plastic sheets.
-
Thermoforming Thermoforming heats a plastic sheet until it becomes flexible, and then forms it into a mold shape using vacuum, pressure, or mechanical means. Upon cooling, the plastic takes the shape of the mold. This method is widely used in the packaging industry for crafting plastic containers, trays, and other packaging materials. Larger applications include car doors, dash panels, and refrigerator liners.
With plastic molding techniques surrounding us in every facet of life, understanding these varied methods is crucial, especially if you're considering manufacturing a product. This knowledge will enable you to select the most suitable method to achieve your manufacturing goals.